虽然从业十数年,可直到2012年的8月参与钢琴国抽工作,我才得以开始大范围地深入了解众多国产钢琴的产品质量。其后,从2012年的9月起至2013年12月,我同国家轻工业乐器质量监督检测中心的同事们一同奔赴各地钢琴生产企业,进行质量检测工作,从了解钢琴的产品质量,进而深入到了解产品质量的成因。16个月的工作,看到国内众多钢琴企业的进步或者衰退,使我感触颇多。
中坚群体
工装、卡具、专用工具大量地使用在当今钢琴厂的生产线上,其中不乏近几年国内技师引入的新东西。除了照搬与日韩合资的企业的生产线布置,欧洲钢琴生产线工人用的装置,美国技师使用的工具,都被借鉴到我们的生产中来。更有一些相似的工装,分别用在不同的厂家,有的是外国技师带来的,有的是中国技师传播开的,想到这些工装是国内外技师智慧结晶的共鸣,我欣喜。这显示出,作为技术个体的中国技师在个人技能方面是完全可以与欧美技师抗衡的。
总体来说,虽然我们的总装技师动手能力很强,熟练度很高,但是对于钢琴制造的基本概念,或者说基本原理,却是非常模糊的。在总装方面,主要体现在制音器开启方面键盘与踏瓣的相对关系,弱音踏瓣行程,琴键下键负荷或回升负荷等方面的调整没有章法。特别是,为了追求音准的相对一致性与稳定性,很多企业都开始使用音准仪或类似设备,这种理念较之过去进步很多,但绝大多数企业并没有自己专署的设备。大家使用的是Yamaha的音准仪或软件,韩国的通用型音准仪,国产将军通用型音准仪,还有未经曲线检定的免费软件。这表明大家还没有理解弦列设计对于音准曲线的影响。
从生产工序来看,差异最大的地方就在于共鸣盘的生产。差异主要表现在两个方面,一个是共振板与框架的粘合时机,一个是配马方式。共振板与框架的粘合时机体现了制造者对于音板设计弧度的理解程度,配马方式体现了制造者对于钢琴共鸣盘设计的忠实程度。我们看到,大多数企业的共鸣盘生产还没有进入到全自动化时代。在不考究的工序之下,半自动化作业铲麻花或者使用电动工具铣肋木,都仅仅起到了美化产品的作用。
这表明,在当今的中国,大多数的企业的生产还不能如实反映设计师的设计,支持大多数钢琴企业生产的中坚力量是总装技师,而非设计师。虽然我们都知道,一架钢琴最关键的技术在于共鸣盘设计与生产。
核心技术
中国特定的经济历史环境,使得我们在还没有充足的时间产生出真正意义上的设计人员的时候,已经是钢琴企业遍地开花了。1980年代那种老企业技术人员被外借协助办厂,1990年代那种请老企业退休技术人员入职办厂,或者2000年代那种老企业技术人员未离职即私下参与办厂的与“设计”较劲的时代已经一去不复返了。几近于无的共鸣盘专利保护加之中国人对于知识产权的不屑,使得共鸣盘的图纸已不是稀罕物。听闻,某大企业曾被技术人员偷偷出售的几万元一张的设计图纸,现在是请一顿“大餐”即可到手。更有各类型号的铁板,被各个铸造厂四处私卖,遍布全国。
打开钢琴上、下门看一看,大家都会知道,中国年产30余万台的钢琴不过是从几张图纸衍化出来的。(看看众多企业争相山寨的是那个品牌的共鸣盘,就知道大家心目中的优秀设计是什么了。)虽然有些企业的设计人员在图纸上修修改改,或者重绘新图,但是终究没有产生出一种具有明确特点的声音来。这不由得大家质疑——纠结于聘请所谓知名设计师是不是由于“名琴必须有独特设计”的这一古老神话的商业操作呢?
如果将钢琴共鸣盘看作一个平面,根据三点确定一个平面的原理,使铁板的4个顶点保持一个平面是比较困难的,铸造中存在一定范围的误差也是可以理解的。但在铁板铸造厂,看到很多款变形严重的铁板要靠工装将其压平,我疑惑了。钢琴的基本结构知识告诉我们,钢琴要靠铁板和背架共同承受十几、二十吨的琴弦拉力。是否可以推断:如果铸造之后铁板翘曲严重,即便是靠工装将其压平,其内应力也必定发生变化。这样的话,靠螺栓固定到背架上的铁板,是否能够良好承受琴弦的强大拉力呢?铸造厂的技术人员告诉我,某些经典型号的铁板变形非常之少,这是不是从侧面证明了我对于“从铁板铸造即可看出设计是否合理”的推断呢?
也许正是在这种现状下,现今中国钢琴界最主流的设计模式从“可听”的转变为“可视”的。也就是说,所谓的设计要让外行能够看到,成为销售人员的卖点。精心设计创造良好音色的努力,远远没有装在琴内的耀目的铁板螺栓创造的利润高,这是当今中国音乐普及匮乏的大环境下中国钢琴设计人员的成功还是悲哀?
在这种现状下,众多的企业直接购得共鸣盘或者铁板,由有经验的总装技师进行装配、生产,也就不足为怪了。这让大家反思:在现阶段的中国,钢琴制造的关键到底是什么?
——毋庸置疑,当代钢琴制造的关键是标准化。这是由产量决定的。
标准化时代
在解决了确保演奏性能的机械结构设计问题——断联(现代钢琴区别于古钢琴的核心技术)——之后,钢琴制造基本可以划分为三个时代:沙龙时代,音乐厅时代,世俗化时代。(当然,钢琴设计与制造的发展趋势总体上就是世俗化趋势。)沙龙时代解决了钢琴的耐用性问题,钢琴开始不再会被轻易弹坏,代表品牌是Bosendorfer。音乐厅时代解决了钢琴的音量问题,钢琴的琴体更大,琴弦张力加大,代表品牌是Steinway。世俗时代解决了钢琴的大工业生产的质量问题,代表品牌是Yamaha。
不得不承认,国人对于Yamaha的评论有失公允。独获天时的企业和Yamaha搞合资,失去天时的企业模仿Yamaha设立生产线,经济实力不充足的企业山寨Yamaha的共鸣盘。大家把Yamaha当作学习的目标,却又极尽品牌排挤之能。无论是厂商还是经销商,都在扬欧洲品牌抑标准化大工业生产模式的Yamaha。殊不知,现今在中国大陆最负盛名的所谓欧洲品牌Steinway只不过是钢琴大工业生产的不完全发展形态。
请看Bosendorfer的介绍:…… 先将这些木材放置于室外约5年使其干燥,再根据木材的种类及用途放置于干燥室12~15周使其干燥至标准含水量……为了使浇铸完成后的铁板完全失去应力,将其放置在室外约半年时间……一台钢琴的制造工期耗时约62周……自贝森朵夫创办180年的悠久历史中,只制造了48,000台钢琴,现在每年的制造数也仅为350台(见 Bosendorfer中文官网 ) 。 可以说,这是一种设计师与技师共同完成设计初衷的手工生产模式。当年产量到达 数千台时 Steinway 的生产周期定为半年,产能最大时较之 Bosendorfer要 提高40余倍。这种情况下,保持设计初衷对于技师的技术要求之高可以想见,而保持手工生产模式的劳动强度对于设计师和技师则是难以想象的,大工业化模式的引入成为必然。也正是在这种历史发展的必然趋势下,保证 年产20余万架 产品品质的 Yamaha标准化大工业生产模式诞生了。
标准化生产模式,简单说,就是生产的一致性。从零部件到成品。只有如此,才能在完成高产量的同时保证产品设计初衷。中国目前的钢琴企业,即便是从技师技能的条件来看能实行Bosendorfer式 设计师与技师共同完成设计初衷的手工模式生产, 也会在售价格决定成本的市场竞争中破产。国内钢琴业现状是,产量不高的企业勉强采用Steinway式不完全钢琴大工业生产模式,却无法达到Steinway的品质;产量高的企业勉强采用Yamaha式的钢琴大工业生产模式,却无法比肩Yamaha产品的品质一致性。
对于自然而言,参差多态是为美;对于钢琴而言,如果同一个设计做出不一致的产品,我们将无法判断“正确”或者“错误”究竟是出现在设计环节还是出现在生产环节。换言之,即便做出了品质优秀的钢琴,也完全是出于偶然。这种随意性不光给我们的生产带来内耗,还给我们的售后带了巨大的压力。仅仅一个键盖无法互换的问题,就不知要耗费企业和零售商多少人力、物力。可以说,在中国钢琴技师技术现有水平和“产量—销售价格”的双重限制下,生产的标准化程度就代表着产品的品质,代表着生产成本。标准化生产是目前大部分中国钢琴企业求发展的唯一途径。
学而不思则罔
资历是一把双刃剑,有可能是我们的财富,也有可能是我们的拦路虎。前苏联出版的《钢琴制造》曾经被业内奉为“宝典”。正是这样一个从未生产出好钢琴的国家的造琴理论曾指导我们生产钢琴很多年。这表明中国的钢琴企业对于技术急切于学习而失之于思索。
同样的原子不同的排列产生出天壤之别的物质——金刚石与石墨;同样的材料不同的工序会做出完全不同的产品。在中国钢琴行业迅速低俗化,像电脑行业一样普遍实行材料标配的时代,也许生产工序恰恰是目前限制中国钢琴企业提升品质的瓶颈。企业对于生产核心技术的理解程度体现在工序设定上,展现在生产线上。也许成本限制了老企业对于设备更新或者厂房改造的投入,为新企业带来了赶超的机遇。但是大多数新企业的生产线设备是新的,意识是老的。这表明大部分钢琴企业对于钢琴制造的认知程度较低,对技术发展的前瞻性不足。也许这是由于企业聘用的技术人才导致的。
企业网罗什么样的技术人才就会为企业注入什么样的技术意识体。作为技师,这些“技术意识体”虽不能改变作为钢琴核心技术的共鸣盘设计,却能左右设计初衷的最终落实情况。老厂的技师将其技术传播到各地,老厂的销售人员也网罗一些技师纷纷建厂。在对技师进行技术复制的同时(且不去讨论这种没有校正程序的复制是否会使技术走样),缺少了一种应有的对于技术的质疑。目前,内部有定期技师规范培训的钢琴企业仅有Yamaha一家。定期做售后技师规范培训的钢琴企业也仅有Yamaha一家。珠江钢琴发展了几十年才在2013年进行了第一次售后技师的常规性培训。国内绝大多数的生产企业和培训机构都还没有意识到规范技术的重要性,没有意识到技术操作不规范对产品质量的影响。
如果说20世纪中国钢琴企业的学而不思体现在迷信《钢琴制造》上,那么21世纪中国钢琴企业的学而不思则体现在大企业盲目巨额聘用售后技师培训工厂技工试图提升企业质量上。目前中国产量最高的钢琴企业年产大约13万台。如果企业打算以量产立足市场,从年产千台发展到年产十数万台,会经历几个瓶颈期,但面对的问题却只有一个——如何在提升产量的同时保证质量。这不是简单的找个技师做做员工培训就能够做到的,这需要的是科学工序之下的高度标准化生产。看到企业中的总装技师有大把的时间扎堆聊天就能明白,现代化管理不是你有多少机器在生产线上,而是对人力的精确计算。
Steinway的厨房
品牌之间免不了比较。面对欧洲琴的时候,我们讲它生产历史长,讲我们有价格优势;面对日本琴的时候,我们说它没有个性,没有欧洲味道。合资企业炫耀外资背景,老企业炫耀资格。德清钢琴,不幸地被其他地方的几乎所有钢琴企业说成是品质最次者,却不提这里也是珠江钢琴的重要基地。这里的钢琴生产被称为“农民造钢琴”,夫妻农闲时节在灶台边做钢琴被大家当作笑谈,却不提Steinway的第一架钢琴正是诞生在厨房之中。
在这一年多的时间里,在四周一片“做大做强”的呼声中,我见到了中国钢琴企业的另一面。怡然自得的一面。父辈创业,将企业交给儿辈,自己乐得清静,闲来用边角料做做木工艺品;父亲开矿,为儿子投资个钢琴厂,让儿子历练;自己家有房屋、土地,池塘边、田地旁悠然做琴……这些没有太多经济压力的企业也就没有太多的产量要求,做起琴来心态要平和一些。不知道他们之中会不会诞生出21世纪的“F azioli ”?
对于普通的使用者而言,钢琴的生产是静态的,对于一个品牌的品质认知,可能仅仅停留于他四处比较、选购时销售人员的概念灌输。对于一个专业从业者而言,钢琴的生产是动态的,换言之,品牌的品质是动态的。设计团队、技师、工序、用材等的改变,自动化设备的使用,甚至一个工装的使用,都会对产品质量产生足够深远的影响。我想,2014年,中国的钢琴企业还会发生不小的改变。
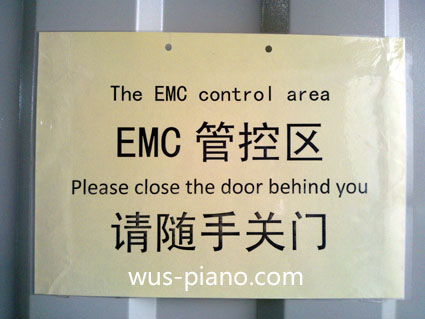
|